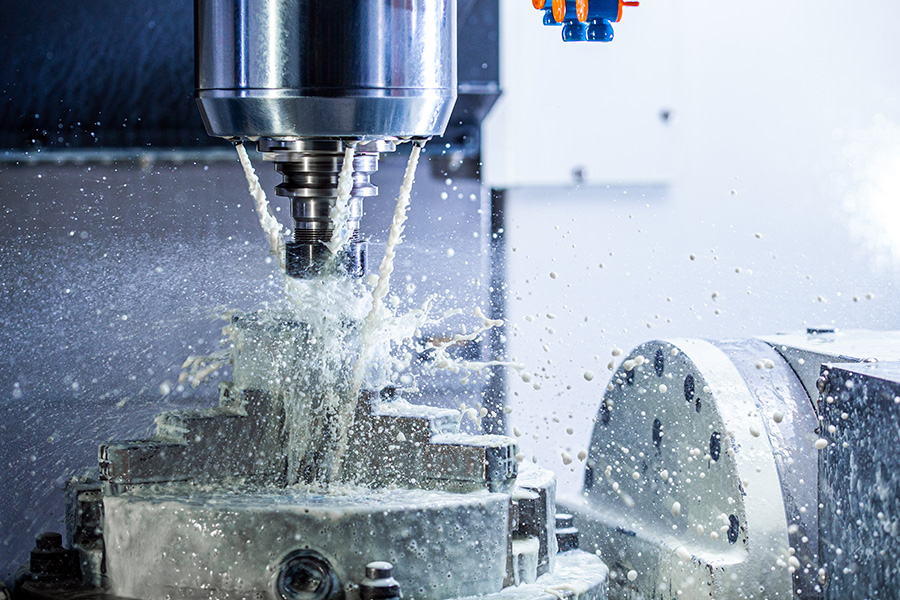
金屬切削液稱為切削液;切削過程中的潤滑可以減少前刀面和切屑.后刀面與加工面摩擦形成部分潤滑膜,降低切削力.摩擦工具與工件毛坯之間的表面溫度和摩擦部分的磨損,提高了工件材料的切割性能。
不同的切削工藝對切削液有不同的要求。對于工件的質量,正確選擇合適的切削液是非常重要的。
粗車削_
粗車加工余量大,切削深度大,進給量大,切削阻力大,切削熱量大,刀具磨損嚴重。應主要用于冷卻,并具有一定的清潔度.潤滑和防銹效果。有效的水基切割液可以及時帶走切割熱量,降低切割溫度,提高工具的耐久性。一般來說,最好使用極壓乳液。極壓乳液不僅具有良好的冷卻性能,而且具有良好的極壓潤滑性能。使用水基切割液時,注意機床導軌表面的維護。工作前,擦干工作臺上的切割液,涂上潤滑劑。
精加工車削_
精車精車時,切削余量小,切削深度一般只有0.05-0.8mm,進給量也很小。確保工件的精度和表面粗糙度。細車切削力小,切削力小。.低溫,低摩擦系數.潤滑性好的切削液。一般采用含油添加劑的高濃度乳化液和切削液(質量分數在10%以上)。菜籽油必須用于高精度的車削,如細螺紋.大豆油或其它產品作為潤滑劑,以滿足精度要求。由于植物油穩定性差,易氧化,
無聊的
鉆孔機理與切割機理相同,但內孔的切割量和速度較小,但散熱條件較差。乳液可以用作切割液。當流動性良好時,應適當增加切割液的壓力。
銑削
銑削是間歇性切割。每個齒的切割深度不時變化,容易產生振動和一定的沖擊,因此銑削條件比車削條件差。高速平銑削或高速垂直銑削需要具有良好冷卻性能和良好潤滑性能的切割液,如極壓乳液。在低速銑削中,需要良好的潤滑切割油,如精密切割油和惰性極壓切割油。不銹鋼和耐熱合金鋼可使用含硫和氯極壓添加劑的切割油。
鉸孔
鉸鏈孔是孔的精加工,精度要求高。鉸鏈孔是一種低速小進給切割,主要是由于工具和孔壁被擠壓和切割,碎片容易留在凹槽或附著在刀片上,影響擠壓效果。破壞加工精度和表面粗糙度,增加切割扭矩,但也會產生碎片腫瘤,增加工具磨損。鉸鏈孔基本處于邊界潤滑狀態。一般來說,潤滑性很好.高濃度極壓乳液或極壓切割油具有一定的流動性,效果良好。高壓復合切割液可用于不銹鋼和耐熱鋼。對于深孔鉸鏈孔,
拉削
拉刀是一種加工工具,根據刀片齒的數量沿軸向排列大量的齒。拉力切割的特點是高精度加工復雜形狀的工作部件。由于拉刀是一種有價值的工具,其耐久性對生產成本有很大的影響。此外,拉力切割是一種精細的加工,對工作部件的表面粗糙度有嚴格的要求。切割阻力大,切割困難,冷卻條件差,容易劃傷工作部件表面,切割液的潤滑和切割性能要求高。國內含硫極壓添加劑的特殊切割油。
以下配方(質量分數)可用于不銹鋼和耐熱合金的拉削:JQ-二極壓潤滑劑20%,氯化石蠟15%,苯801%,L-ANN系統油損耗64%。
鉆孔_
普通的扭曲鉆是粗糙的加工。鉆孔時,切割芯片難以去除,切割熱難以去除,往往導致刀片退火,影響鉆頭的使用壽命和加工效率。選擇性能良好的切割液可以延長鉆頭的使用壽命幾倍以上,生產效率也可以顯著提高。一般來說,可以使用極壓乳液或極壓合成切割液。極壓合成切割液表面張力低,滲透性好。它可以及時冷卻鉆頭,非常有效地延長工具壽命,提高加工效率。對于不銹鋼、耐熱合金等困難的材料,
螺紋加工
切割螺紋時,刀具與切割材料呈楔形接觸,切割刃的三面被切割材料包圍。切割扭矩大,難以清除碎片。芯片不能及時帶走熱量。刀具容易磨損,鋸末堵塞,容易振動。尤其是攻絲時,切割條件要求高,有時會坍塌.斷絲錐的情況。
螺紋加工
切割液必須具有較低的摩擦系數和較高的極壓力,以減少工具的摩擦阻力,延長工具的使用壽命。一般來說,應選擇含有油性劑和極壓劑的復合切割液。此外,切割液在攻絲過程中的滲透性也非常重要。切割液是否能及時滲透到切割葉片中,對絲錐的耐久性有很大的影響。切割液的滲透性與粘度有關。低粘度油具有良好的滲透性。必要時,可以添加少量的柴油或煤油,以提高滲透性。在某些情況下,切割液很難進入盲孔。在這種情況下,
用切削液攻絲的公式如下:
10%硫酸化脂肪油,10%氯化石蠟,8%脂肪油,L-AN鋼及合金鋼攻絲螺紋全損失72%。
JQ-20%的極壓潤滑油,JQ-10%精密切削潤滑油,L-AN全損系統油70%,適用于鋼和合金鋼攻絲。
JQ-2極壓潤滑油15%,柴油機油20%,L-AN全損系統油65%,適用于鋁及鋁合金攻絲。
JQ-2極壓潤滑油30%,氯化石蠟10%,脂肪油10%,L-AN全損系統油50%,適用于不銹鋼和盲孔攻絲。
20%乳化油+80%適用于鋼標準件的螺紋加工。
研磨
研磨可以獲得較高的尺寸精度和較低的表面粗糙度。研磨速度高,熱量大,研磨溫度可達8-1萬-1萬℃甚至更高。由于熱應力,容易造成工件表面燒傷、表面裂紋和零件變形。砂輪磨損鈍化,磨粒脫落,磨屑和砂輪粉容易濺到零件表面,影響加工精度和表面粗糙度。在加工韌性和塑料材料時,磨屑容易卡在砂輪工作面的縫隙中,或磨屑與加工金屬熔化在砂輪表面,使砂輪失去磨削能力。因此,為了降低磨削溫度,沖走磨屑和砂輪粉,提高磨削比和工件表面質量,必須使用具有良好冷卻和清洗性能的切削液,具有一定的潤滑性和防銹性。
1.普通磨削:
防銹乳液或蘇打水及合成切削液(質量分數)可用于2%防銹乳液.亞硝酸鈉0.5%.碳酸鈉0.2%.水97.3%.0.3%碳酸鈉.0.5%甘油.98.6%水;直接使用3%-4%的防銹乳液或化學合成液。
精度要求高精度磨削,精度要求高精度磨削,H-加工精度和研磨效率為4-5%,使用濃度為4-5%。
2.高速研磨:
砂輪速度超過50m/s磨削通常稱為高速磨削。磨削溫度隨著砂輪線速度的增加而顯著增加。試驗后,砂輪線速度為60m/s磨削溫度(平均工件溫度)比3000m/s砂輪線速度為80%;m/s當磨削溫度高于60時m/s時間。高出15-20%。砂輪線速度提高后,單位時間內參與研磨的研磨顆粒數量增加,摩擦力增加,能耗增加,工件表面溫度升高,表面可能出現燒傷和裂紋。使用冷卻性能高的冷卻液。因此,普通研磨液不應用于高速研磨,而應用于滲透性好、冷卻性能好的高速研磨液。GMY高速磨削液滿足6速6萬m/s高速磨削工藝要求。
3.動力研磨:
這是一種先進的高效研磨工藝。例如,在切入式高速強磨中,線速為60m/s的砂輪將以3.5-6mm/min徑向切割進給速度。速度可達20-40mm3/mm.s。這時,砂輪研磨顆粒與工件之間的摩擦非常劇烈。即使在高壓大流量的冷卻條件下,摩擦區工件表面的溫度范圍也在700-1萬之間℃。不,研磨過程是不可能的。與乳液相比,推力研磨總量增加35%,研磨比增加30-50%,正常研磨時間增加40%左右。功率損失約為40%。因此,冷卻液的性能對強磨的研磨效果有很大的影響。目前,中國生產的強磨液有QM高速強力磨削液和HM慢慢地進入強磨削液。
4.金剛石砂輪磨削:
硬質合金.